Northwest Skills Institute Provides Essential Training to Apparel Industry
A partnership between Northwest Skills Institute & BC Alliance for Manufacturing
Apparel is the fourth largest component of manufacturing in British Columbia. The design element is even larger. Vancouver is home to many global brands for performance and technical apparel as well as premium fashion. Arc’teryx, Aritzia, Herschel Supply, lululemon, MEC, and Ryu are some of the firms that have grown up here.
The industry is facing significant skills shortages due to exponential growth and demographic shifts. The industry has a labour replacement rate of 135% by 2025. This means every worker needs to be replaced and one-third new positions also require people. This critical skills shortage is forcing many apparel businesses to close while some make the choice to relocate to the United States.
“The program successfully certified and placed 500 individuals for apparel occupations.”
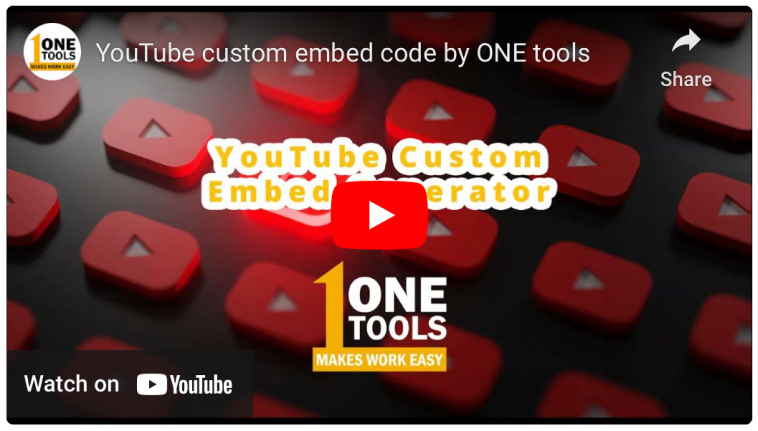
The Challenge
Technical trades such as industrial sewing machine operator, sample sewer, and pattern maker are the jobs that are the foundation of the industry. Without them designers cannot get samples made or seasonal production manufactured.
In 2019, the industry is already short 3,000 industrial sewers. These are occupations where higher skills lead to higher quality and the ability to produce more complex products. Unfortunately, no local training program exist to create the next generation of apparel trades people required immediately.
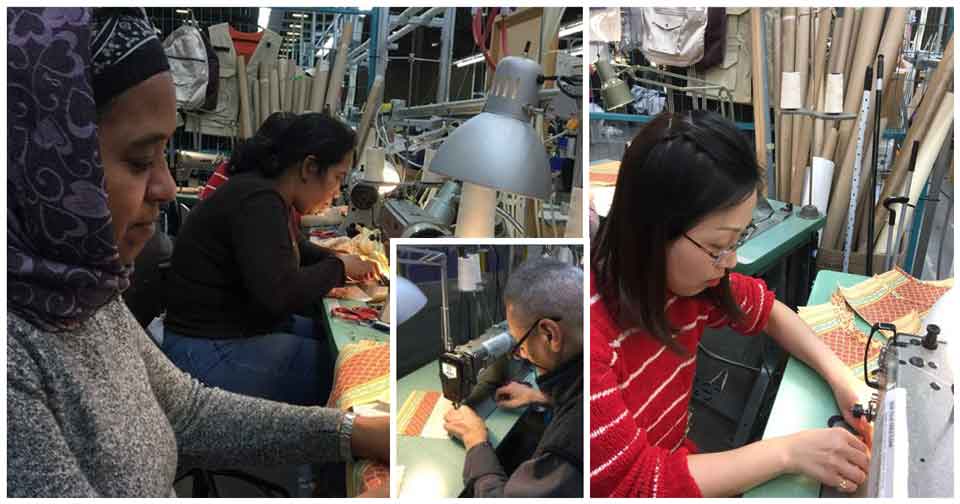
The Outcome
BC Apparel and Gear Association asked The Northwest Skills Institute (NW Skills) to develop a training bootcamp that could take non-sewers and give them the skills to succeed in the industry. NW Skills worked with industry to determine the types of skills that new workers would need to be successful across a diverse range of fabric and product types. NW Skills also worked with employers to determine a quality standard for three levels of industrial sewer. A training program was launched in two rented factories to begin the process to build a pathway to fill the many vacancies employers are struggling with. Employers welcomed the fact that their industry organization and NW Skills we addressing the fact that the industry needed workers in order to survive and grow.
Take Away
To date, the IST program has placed well over 500 individuals in careers with employers in the apparel industry. The training model was well received and has been shared with other apparel jurisdictions so they can also address their own local skills shortages.
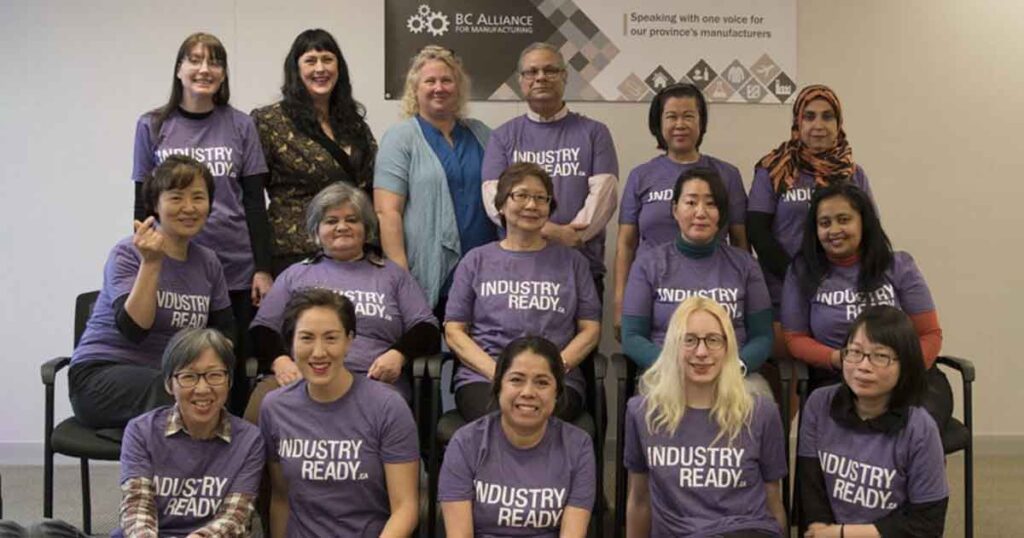
Being Industry Ready is what makes the difference
Industry Ready empowers students and keeps industries robust and thriving by providing an engaged and skilled workforce. Talk to us to find out more about opportunities for certifications!